IGD were recently approached by one of our Mechanical and Electrical (M&E)contractors to provide nitrogen dioxide detectors for a delivery sorting depot in North Worcester. The project required 26 nitrogen dioxide detectors and we chose to utilise our ground-breaking TOC-750 addressable systems. Read on to find out why the delivery sorting depot required nitrogen dioxide detectors. Plus learn more about the benefits of using our industry-leading technology.
Why Did the Sorting Depot Require Nitrogen Dioxide Detector?
The delivery sorting depot required several nitrogen dioxide detectors positioned near the delivery vehicle drop off points, where the delivery vans would empty the parcels onto conveyor belts. The site is required to monitor for nitrogen dioxide (NO2) as it is classed as a toxic gas under HSE and COSHH regulations. The exposure levels for NO2 are the following:
Short Term Exposure (15 minutes) – 1ppm
Long Term Exposure (8 Hours TWA) – 0.5ppm
The sorting depot uses diesel-powered vehicles. One of the main exhaust gases from diesel-powered vehicles is nitrogen dioxide. While the parcels are being emptied the delivery vehicles are still running. This poses a significant health risk for the workers unloading the vans. This is because the van’s exhausts are pointing inside the depot; therefore it was essential that nitrogen dioxide detectors are installed to measure for any dangerous rises in NO2. In addition, the nitrogen dioxide detector is also needed to control the ventilation rate based on the gas level present.
As an independent gas detection manufacturer with over 100 years of leading innovation in the gas detection industry, International Gas Detectors were approached to provide a nitrogen dioxide detector system for the depot. They also requested we provide a flexible system as cable space was at a minimum.
IGD rose to the challenge and utilised our years of experience and new technology to provide the client with a cost-effective, flexible, and innovative solution.
Nitrogen Dioxide Monitoring Solution
As part of our customer focused approach, we provided our M&E contractor full project support. Our technical sales team attended site to asses not only where the nitrogen dioxide detectors would need to be located; but also the quantities required. In addition, we spoke with the sorting depot team, to gain an understanding of their requirements and where best to position the control panel. After the site visit, our team provided full site-marked drawings and proposed wiring diagrams to illustrate how the system was to be installed.
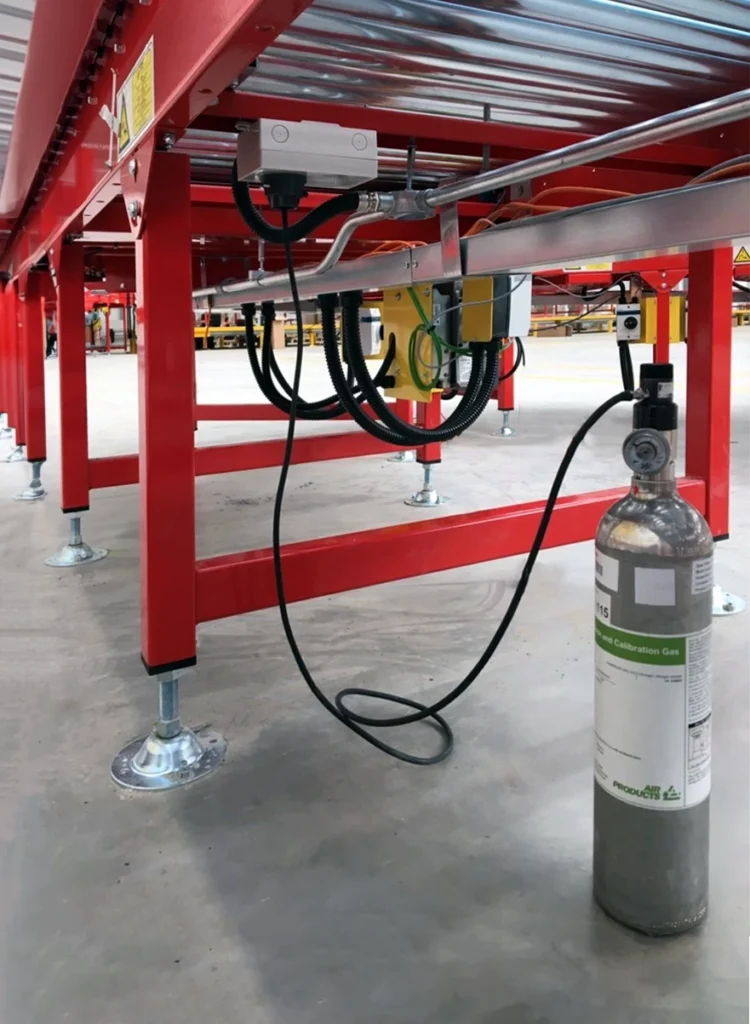
One of the major concerns from both the sorting office and our M&E contractor was the limited cable space available, as the nitrogen dioxide detectors would be fitted underneath the conveyor belts. This is a major stumbling block and a costly one seen on older 4-20mA analogue systems. As each detector or ancillary device must be wired straight back to the control panel. This meant you could end up with bulky and expensive cable bundles. This would not have fit underneath some of the conveyor belts. However, our 750 series 2-Wire Addressable technology, means each sensor is daisy-chained together on a radial from the controller (also known as a cable highway). The cable highway only uses a 2-Core cable to provide the sensors with both power and communication. This not only drastically reduced the installation cost for the M&E contractor, but it also means that we had plenty of room under the conveyor belts.
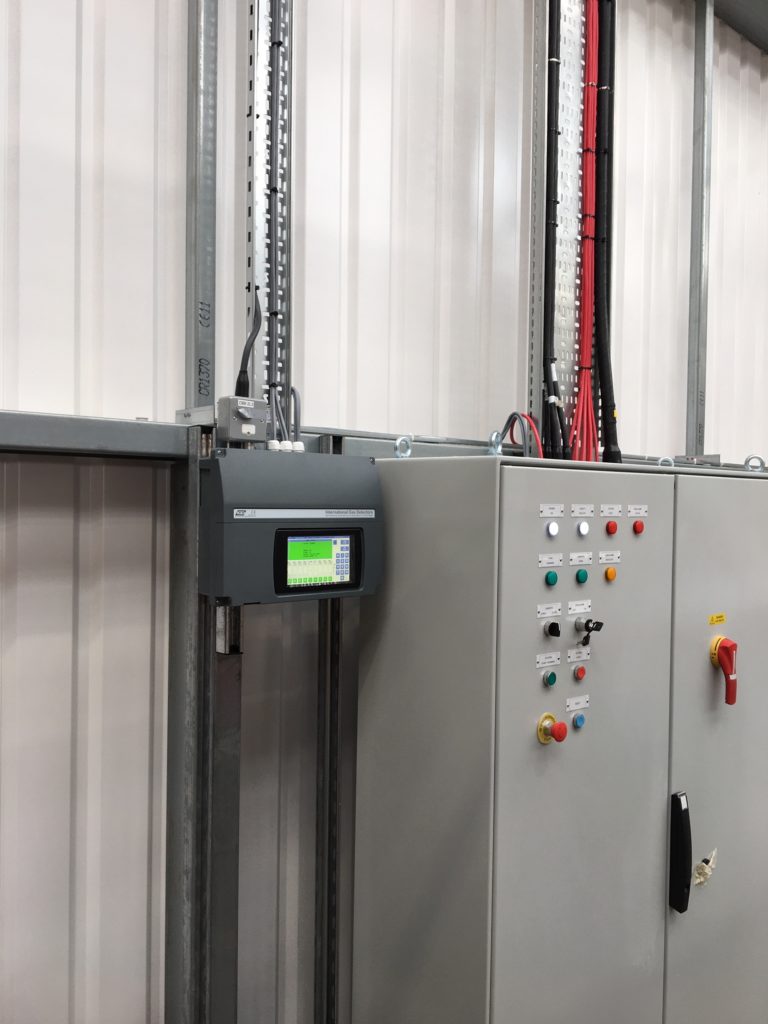
The client opted to utilise our TOC-750 Series Control panel and TOC-750 Series Addressable Safe Area, nitrogen dioxide detectors. The 750 Series Control Panel has 4 cable highways for maximum installation flexibility. Having this flexibility enabled our M&E contractor to utilise each cable highway to be run underneath each conveyor belt. This reduced the requirement for long cable runs and ultimately reduced the installation cost. In addition, the colour touchscreen HMI display provides the sorting depot’ safety team with live gas readings and an easy to use interface.
Finally, the TOC-750 control panel comes with relay outputs and ModBus as standard. This meant the sorting depot could easily integrate its ventilation system to the 750 Series Control Panel. With the TOC-750 user-friendly interface, we could customise which alarm level triggered their desired ventilation speed. In addition, we supplied illuminated signs stating “SHUT OFF ENGINES” if the gas alarms would not reset. This provided the delivery drivers with a clear visible instruction. This was all done using our intuitive and configurable cause and effect.
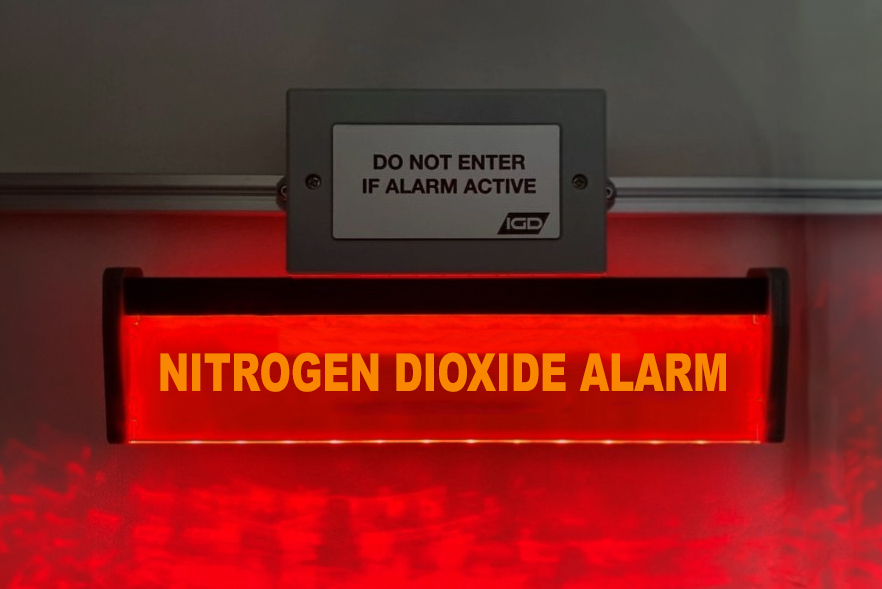
Nitrogen Dioxide Detectors: The End Result
We were able to install the TOC-750 nitrogen dioxide gas detector system at a very competitive price, as the system only uses a 2-Core cable, interconnecting the detectors together on a radial. This provided a 70% saving both for our M&E contractor and within budget. The 750 system exceeded the client’s expectations with our advanced 2-Wire Addressable technology. In addition, we provided the client with a full commissioning report and have now become the preferred supplier for our M&E contractor, due to the support received by IGD.
If you require a nitrogen dioxide detector or a gas detection system, get in touch with our team to learn more.